在防弹衣、航空航天复合材料、光纤增强材料等高端领域,芳纶(Aramid Fiber)始终扮演着“材料之王”的角色。这种强度比钢丝高5倍、重量却仅为钢材1/5的超强纤维,其性能的秘密不仅在于复杂的纺丝工艺,更始于上游原材料的精准选择。究竟哪些关键物质支撑了芳纶的诞生?这些原料又如何影响最终产品的性能?
一、芳纶的分类与核心原料体系
芳纶分为对位芳纶(如Kevlar)和间位芳纶(如Nomex)两大类,两者因分子链结构差异而性能迥异,但均以芳香族化合物为核心原料。
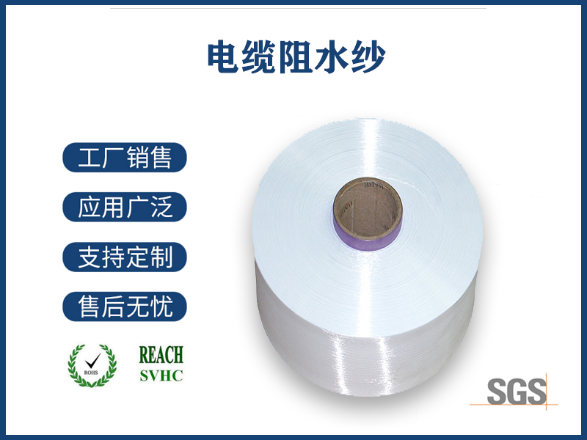
- 对位芳纶的“黄金配方”:聚对苯二甲酰对苯二胺(PPTA)
对位芳纶的原料体系围绕对苯二甲酰氯(TPC)和对苯二胺(PPD)展开。这两种单体在低温溶液缩聚反应中形成PPTA聚合物,其分子链的刚性排列赋予纤维超高强度与耐热性。
关键数据:全球约70%的对苯二甲酰氯产能集中于中国,而高纯度对苯二胺的生产则被少数化工巨头垄断,直接牵动芳纶产业链的稳定性。
- 间位芳纶的“柔性密码”:聚间苯二甲酰间苯二胺(PMIA)
间位芳纶的原料组合为间苯二甲酰氯(IPC)与间苯二胺(MPD)。由于分子链呈锯齿状排列,这类纤维在阻燃性和柔韧性上表现更优,广泛应用于消防服和高温过滤材料。
二、上游原材料的制备技术与挑战
芳纶原料的合成高度依赖氯化反应和胺化反应,工艺控制直接决定单体的纯度与成本。
- 对苯二甲酰氯:光气法的替代革命
传统工艺使用剧毒光气(COCl₂)进行氯化反应,存在安全与环保风险。近年来,非光气法(如氯苯溶剂法)逐渐兴起,通过氯化亚砜或三氯氧磷替代光气,降低生产门槛。
- 高纯度芳香胺的提纯难题
无论是PPD还是MPD,其纯度需达到99.9%以上才能满足聚合要求。行业普遍采用重结晶与分子蒸馏技术,但设备投资高昂,导致中小型企业难以进入上游市场。
三、中间体供应链的全球格局
芳纶原料的供应呈现明显的区域集中特征:
- 对苯二甲酰氯:中国凭借成熟的煤化工产业链占据主导,2022年全球市场份额超65%;
- 间苯二甲酰氯:日本宇部兴产、美国杜邦等企业掌握核心专利,技术壁垒较高;
- 芳香胺类:欧洲化工巨头(如朗盛、巴斯夫)通过垂直整合模式控制从苯系物到胺类产品的全链条生产。
行业洞察:近年来,中国企业在间位芳纶原料领域加速突破,例如浙江闰土股份的间苯二胺产能已跃居全球前三,逐步打破海外垄断。
四、原材料创新推动芳纶性能升级
为满足5G通信、新能源电池等新兴需求,原料端的改性研究成为行业焦点:
- 共聚单体引入
在PPTA聚合过程中添加第三单体(如含氟苯环化合物),可提升纤维的耐酸碱性。荷兰帝斯曼的Twaron Black系列即通过此技术实现抗紫外线性能跃升。
- 生物基原料替代
杜邦公司与美国能源部合作开发的生物基对苯二甲酸(来自玉米秸秆),已成功试用于Kevlar生产,碳足迹减少40%。
五、环保政策与循环经济的影响
随着欧盟REACH法规、中国“双碳”目标的推进,芳纶原料生产面临双重压力:
- 废弃物回收:间苯二甲酰氯合成中产生的盐酸需通过闭路循环系统回收利用,否则单吨成本将增加12%-15%;
- 绿色工艺替代:采用离子液体催化剂替代传统有机溶剂,可减少90%的VOCs排放,但设备改造成本仍是中小企业的主要障碍。
从这一视角看,芳纶上游原材料的竞争已不仅是技术与产能的比拼,更是可持续发展能力的较量。