在纺织工业的浩瀚星空中,涤纶长丝如同一颗璀璨的明珠,凭借其高强度、耐磨损、易染色等特性,成为服装、家纺、工业用布等领域的“隐形支柱”。据行业数据显示,全球涤纶长丝年产能已突破6000万吨,占据合成纤维市场的半壁江山。然而,这一看似寻常的纤维背后,究竟隐藏着怎样的生产奥秘?本文将以涤纶长丝的生产流程与核心工艺为脉络,揭开其从化学原料到优质纤维的蜕变之旅。
一、涤纶长丝的“诞生起点”:聚酯切片与原料处理
涤纶长丝的原料是聚对苯二甲酸乙二醇酯(PET),通常以颗粒状的聚酯切片形式存在。这些切片的纯度、分子量分布及结晶度,直接影响最终纤维的品质。生产前需对切片进行严格干燥处理,将其含水量控制在50ppm以下,以避免高温熔融时发生水解反应,导致分子链断裂。
现代工艺中,真空转鼓干燥机与充填式干燥塔是主流设备。前者通过低温除湿减少能耗,后者则利用热风循环实现高效脱水。干燥后的切片被送入螺杆挤压机,在*270-290℃*的高温下熔融为粘稠液体,为后续纺丝奠定基础。
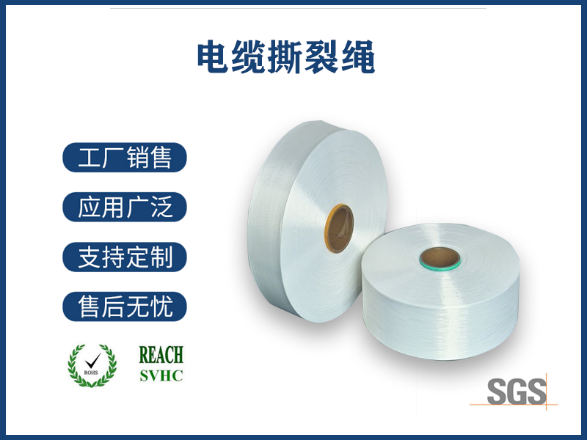
二、熔融纺丝:液态到固态的精密转换
熔融纺丝是涤纶长丝生产的核心环节,其本质是通过精密控制温度、压力与冷却条件,将液态PET转化为连续固态纤维。这一过程依赖三大关键技术:
- 螺杆挤压机的稳定性:螺杆转速与温度梯度需精确匹配,确保熔体均匀流动;
- 喷丝板设计:孔径、孔数及排列方式决定纤维的细度与截面形状,例如圆形孔用于常规长丝,异形孔可生产吸湿排汗纤维;
- 侧吹风冷却系统:冷风温度(20-25℃)与风速(0.3-0.6m/s)直接影响纤维的结晶度与取向度,进而影响力学性能。
*高速纺丝技术(纺速≥4000m/min)*的普及,显著提升了生产效率,同时赋予纤维更高的取向结构,减少后续拉伸工序的负担。
三、拉伸与定型:赋予纤维“钢筋铁骨”
刚从喷丝板挤出的初生纤维分子排列松散,需通过多级拉伸与热定型强化其结构。拉伸工艺分为两步:
- 预拉伸:在玻璃化温度(70-80℃)附近进行,使纤维初步取向;
- 主拉伸:在*120-180℃*的高温下进一步拉伸,分子链沿轴向高度排列,强度提升3-5倍。
随后的热定型采用松弛或紧张模式:
- 松弛定型可消除内应力,提高纤维尺寸稳定性;
- 紧张定型则用于生产高模量工业丝,如轮胎帘子线。
这一阶段中,*在线张力传感器*与*红外温度监控系统*的应用,实现了工艺参数的实时闭环调控,将产品CV值(不匀率)控制在1%以内。
四、后处理工艺:功能化与差异化的决胜战场
为满足市场多样化需求,涤纶长丝需通过后处理赋予特殊功能:
- 加弹工艺:利用假捻变形技术,将直丝转化为蓬松柔软的DTY(拉伸变形丝),用于针织面料;
- 共混改性:添加抗菌母粒、阻燃剂等功能助剂,生产医用防护服或消防织物;
- 表面涂层:通过等离子体处理或化学接枝,改善纤维亲水性,提升染色均匀度。
*绿色生产工艺*成为行业焦点。例如,采用闭环回收系统将废丝重新造粒,使原料利用率超99%;或使用生物基PTA(对苯二甲酸)替代石油基原料,减少碳足迹。
五、智能化浪潮:涤纶长丝生产的未来图景
随着工业4.0的推进,涤纶长丝生产线正加速迈向智能化:
- 数字孪生技术:通过虚拟仿真优化工艺参数,缩短新品研发周期;
- AI视觉检测:实时识别并剔除毛丝、僵丝等瑕疵,良品率提升至99.8%;
- 能耗管理系统:利用大数据分析,将吨丝能耗从*1200kW·h*降至800kW·h以下。
这场技术革命不仅降低了生产成本,更推动涤纶长丝从“量大价廉”向“高质定制”转型。例如,汽车轻量化趋势催生的超细旦高强丝(单丝纤度≤0.3dtex),其断裂强度可达8.5cN/dtex,堪比钢丝。
从实验室到生产线,从传统制造到智能工厂,涤纶长丝的生产工艺始终在创新中迭代。而掌握这些核心技术的企业,正悄然改写全球纺织产业的竞争格局。